Mastering Project Specifications in Construction: Dos and Don’ts for Success
Let’s jump in and learn:
- Importance of Project Specifications
- Understanding Different Types of Project Specifications
- Key Components of a Construction Specification Document
- Common Mistakes in Project Specifications
- Tools and Software for Creating and Managing Project Specifications
- Project Specification Usage Key for Building Success
Importance of Project Specifications
Project specifications provide a detailed description of the materials, quality, standards, and schedule for a building project. Architects, engineers, and specifiers put together the various components of a project specification package. The contract specifications are sometimes created as part of the contract documentation, and other times, they are put together as part of the handoff information.
The importance of project specification documentation in project fulfillment can not be overstated. It protects stakeholders from risk by ensuring that clients, designers, and contractors have the most accurate and current information and also facilitates communication. Poor communication and failure to align on construction details cause major change orders, schedule delays, and cost overruns that reflect poorly on all vendors, regardless of who is to blame.
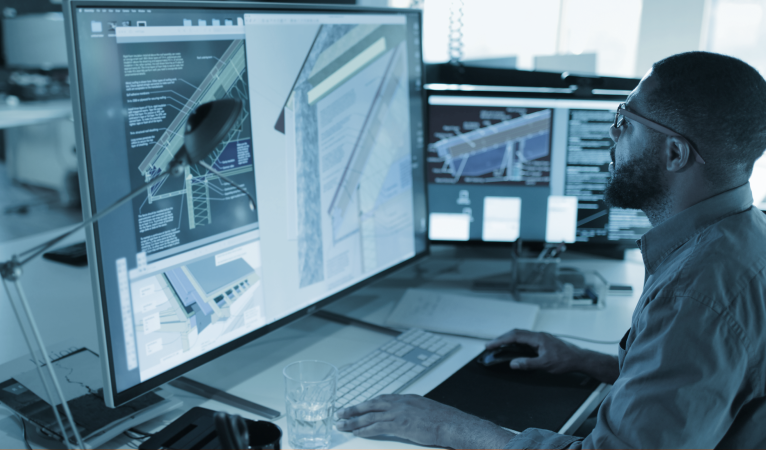
By providing detailed plans that describe precisely what contractors and subcontractors are expected to deliver, project specification documents offer tremendous value in a number of areas, including the following.
Quality assurance
Project specification documents ensure that the project meets the required quality standards by detailing exactly what materials, construction techniques, and performance criteria are expected.
Material selection
Detailed material specifications help avoid issues with substitutions of inferior or inappropriate materials that affect the intended quality of the project.
Regulatory compliance
Project specification documents help ensure that construction teams maintain compliance with a complex web of building codes, regulations, and industry standards.
Risk management
By outlining safety measures, quality control processes, and performance standards, construction specification documents help mitigate risks by reducing the likelihood of accidents, defects, or project failures.
Fine-tune costs
Because project specifications require architects and designers to define the materials and methods they want, it is easier to determine actual costs for materials and labor by developing quotes based on very detailed information.
Increase efficiency
Providing contractors and subcontractors with all the details and intentions for construction projects makes the process faster and the results more accurate.
Additional reasons that project specification documents are important are:
- Establish consistent expectations
- Contribute to the overall organization and success of a building project
- Articulate details about expectations for installations and the quality of workmanship
- Define the precise materials and manufacturers’ products to use for a project
- Identify requirements for installation, testing, and handover
- Set clear instructions on project intent, performance, and construction parameters
- Serves as a key part of an audit trail to address subsequent issues or prove compliance with regulations
Understanding Different Types of Project Specifications
There are three main types of project specification documentation—prescriptive, performance, and proprietary. Each can be used at different stages of a project and supports various types of projects.
Prescriptive project specifications
Prescriptive project specifications are detailed instructions on how to execute a project. They help designers maintain a high degree of control over the process and outcome. While performance project specifications give more authority to contractors, architects and engineers have more control over prescriptive project specifications because they establish a set of rules that should be followed for each project component.
Prescriptive project specifications provide details about how to execute a project, including materials the contractors may use, the process for measurement and installation, and the quality expectations for the project. Three sub-types of prescriptive project specifications are general provisions, required products, and execution procedures.
1. General provisions outline regulations and codes that govern the project and final outcome and detail product handling, required submittals, design requirements, and quality control guides.
2. Required products specify which materials and tools are necessary to complete the project as designed and describe the different materials required for each task and the performance and structural requirements for each in detail.
3. Execution procedures explain how contractors and subcontractors are to prepare the materials, perform and manage the installation, and test the quality after completion.
Performance project specifications
Performance project specifications detail the operational requirements (i.e., functionalities and features) necessary to complete a project with a focus on the outcome rather than the process of achieving it. This approach allows contractors and subcontractors to be more flexible and creative license when determining the best way to execute the project as opposed to letting the architect or engineer dictate these details.
With performance project specifications, contractors are not given information about how to execute the project. They are expected to determine the best methods and materials to achieve the agreed-upon outcome.
Proprietary project specifications
Proprietary project specifications are used when a specific product is being installed, such as a particular type of siding or window. Unlike prescriptive and performance project specifications, which are developed by an architect or designer, proprietary project specifications are created by manufacturers. These documents outline exactly how to use or install the product as well as what other resources are compatible with it.
Key Components of a Construction Specification Document
Construction specification documents contain several key components that are used to direct a project so that it aligns with the design team’s intentions and the client’s expectations.
Agreement
A construction project agreement includes the agreed-upon total price for the project and defines the terms that will govern the entire construction process. The agreement forms the basis from which all other project details, from kickoff to completion, such as scope and schedule, are defined and developed.
The signed agreement is the foundational document for a construction project. All other documents and addendums are referenced in the agreement and are considered part of the agreement.
Bill of quantities
The bill of quantities provides an itemized forecast of the cost of materials, labor, and other expenditures associated with the project. Contractors use this to prepare and ensure the accuracy of project bids. Clients use the bill of quantities to evaluate bids from different contractors.
Construction drawings
Serving as the visual representation of a project, construction drawings provide details and dimensions of the desired end result. Construction drawings illustrate the architect’s vision for the project.
Architects produce a variety of drawing types to illustrate details of the work from different perspectives and for different trade specialties or systems. Examples of construction drawings include:
- Column drawings
- Detail drawings
- Electrical drawings
- Elevation drawings
- Floor plans
- Penetration drawings
- Reflected ceiling plan
- Sections
- Structural drawings
General Conditions
The general conditions guide the execution and management of a construction project, acting as a rulebook for all parties. This component of a construction specification dictates the procedural guidelines and establishes the rights and obligations of the parties involved.
The general conditions specify requirements for insurance and bonds, provide instructions for conflict resolution, and set terms for potential project termination. In addition, the general conditions address the contractor’s operational scope, including the provision of a site superintendent, project management, and the handling of on-site conditions such as security and safety measures. Other areas covered with general conditions are:
- Guidelines for submittals
- Procedures for change orders
- Project administration
- Protocols for payment applications
- Responsibilities of the owner and contractor
Schedule
The construction schedule is a contract document that outlines the project’s timeline and phases. It provides a detailed sequence of activities and establishes critical milestones. The construction schedule is updated to keep it aligned with the work being done and to accommodate any changes.
Schedule of Values
The schedule values (SOV) is an itemized list of work segments with the corresponding value of each one. Throughout the project, the contractor will create a document that shows the percentage of each work item that is complete and the expenditures for each category.
Scope of work
The scope of work describes the tasks that need to be performed as part of the project, the expected outcomes, and the roles and responsibilities of each involved party, such as contractors and subcontractors. It is within the scope of work that specifics about the materials to be used, the standards of workmanship expected, the equipment needed for installation, and other operational details are included.
Special conditions
The special conditions are usually appended to the General Conditions, providing custom elements that require special attention, such as sustainability requirements to comply with green building standards, site security requirements, traffic handling during construction, or adherence to local regulations.
Specifications
Specifications, often referred to as specs, contain the project’s technical data, material requirements, and construction methods. These documents complement the construction drawings, describing detailed project attributes, establishing quality standards for the work, and ensuring adherence to industry standards.
For large construction projects, the specifications are often organized according to CSI MasterFormat or CSI divisions. In this case, a spec book is created with sections detailing the materials and methods for each part of the project, such as:
- Applicable codes, regulations, and/or standards—all applicable local, state, and national building codes, standards, and regulations
- Materials—type, grade, size, color, brand, and other characteristics
- Methods of installation—specific techniques and methods for installing different systems or components
- Quality of workmanship—the standard of work expected from the contractors that often includes references to industry standards, practices, or specific procedures
- Testing requirements—tests that must be conducted on materials or completed work to measure adherence to quality standards
- Timeline and important project milestones—estimated duration of the project key points in the project when certain tasks or stages should be completed
Common Mistakes in Project Specifications
Project specifications are a highly effective tool when used and created correctly. However, errors and poor practices can undermine their value. Understanding these common mistakes in project specifications helps avoid confusion, delays, and costly rework. The following are several of the most common mistakes.
- Failure to update specifications when changes occur
- Formatting errors
- Incomplete or incorrect information
- Inconsistencies and contradictions in different sections of the construction specification documents
- Lack of collaboration with stakeholders when creating the construction specification documents
- Not following standards for specifications, such as MasterFormat, SectionFormat, and PageFormat
- Poor review and editing processes
- Reuse of specifications from a past project
- Use of a proprietary specification when a nonproprietary specification is required
- Vague or ambiguous language
Dos for Creating Effective Project Specifications
A project specification should be developed by the architect or designers with support from project engineers who can provide technical knowledge. For large, complex construction projects, these teams should engage project specification writers who have the experience necessary to ensure all details are included and articulated correctly.
When writing a project specification, begin by reviewing expectations with the client. This helps establish alignment on the performance requirements of the whole project.
Keep the following “dos” in mind when creating a project specification.
Pay attention to content and style
- Write in a way that is easy to understand.
- Use clear, unambiguous verbiage.
- Avoid technical jargon and industry-specific acronyms
- Define any terms that may be unfamiliar to any stakeholder.
Be comprehensive
- Cover all elements of the project, including materials, methods, quality standards, and installation requirements.
- Include detailed information about the materials to be used, such as manufacturer’s specifications, product approvals, and testing requirements.
Maintain consistency
- Use consistent terminology and formatting throughout the document.
- Ensure that specifications align with other project documents, such as drawings and contracts, to avoid conflicts and confusion.
Best Practices for Organizing and Structuring Project Specifications
- Adhere to industry standards
- Begin project specifications early
- Create a clear document hierarchy
- Ensure that all construction specification documents are comprehensive
- Implement defined change order processes
- Incorporate supporting documents
- Keep documents current and comprehensive
- Leverage past projects when writing construction specification documents
- Proofread all construction specification documents carefully
- Review all details to confirm that everything is correct
- Save construction specification documents in a cloud storage system that is accessible to all stakeholders
- Use clear and concise language
- Use software tools to create and manage construction specification documents
- Use standard structure, terminology, and style
Tools and Software for Creating and Managing Project Specifications
There are many options for project specification tools and software. Most experts agree that regardless of which is selected, some type of software package is necessary to effectively create and manage construction specification documents. Project specification tools streamline the process of creating and maintaining project specification documents and improve collaboration throughout a project to optimize performance and outcomes.
Several key considerations when looking for project specification software are reviews and integration capabilities. Reviews give valuable insights into the software’s performance and reliability based on first-hand experiences. It is also important to understand what other tools the system can work with, such as estimating tools, collaboration tools, building information modeling (BIM) systems, project management software, and communication platforms.
Among the many construction specification software tools available, the following are several of the more widely used packages.
Here are some of the top construction specification software tools:
- BIM 360 by Autodesk Specification Management Software
- CMiC Specification Management Software
- DocXellent Specification Management Software
- Finalcad Specification Management Software
- Newforma Project Center Specification Management Software
- Oracle Aconex Specification Management Software
- Procore Specification Management Software
- Projectmates Specification Management Software
- Viewpoint Team Specification Management Software
Project Specification Usage Key for Building Success
Project specification documentation provides the clear scope and details that are the cornerstones of a successful building project. They support cross-team communication, accountability, and effective project management, which are must-haves to ensure that construction projects are completed on time, within budget, and meet clients’ expectations.
Egnyte has experts ready to answer your questions. For more than a decade, Egnyte has helped more than 17,000+ customers with millions of users worldwide.
Last Updated: 16th July, 2024