Good Manufacturing Practice
Good manufacturing practice (GMP) is a set of guidelines and rules that help manufacturers of products, such as cosmetics, food, diagnostics, medical devices, or pharmaceuticals, better protect consumers from exposure to potentially harmful ingredients or processes. Complying with good manufacturing practice is mandatory in all pharmaceutical manufacturing and most food processing.
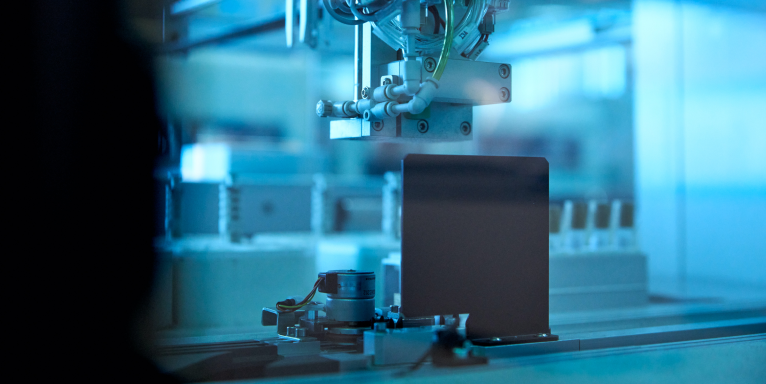
Let’s jump in and learn:
What Is GMP?
GMP is a system that consists of guidelines for processes, procedures, and documentation that ensures manufacturing products are consistently produced and controlled according to set quality standards. It helps ensure that a product is made according to industry standards.
Good manufacturing practice influences the safety and quality of products by requiring manufacturers to address specific areas of production, including:
- Building and facilities
- Complaints
- Documentation and recordkeeping
- Equipment
- Inspections and quality audits
- Personnel
- Quality management
- Raw materials
- Sanitation and hygiene
- Validation and qualification
GMP Regulations
GMP regulations are mandated and enforced in the countries where manufacturers operate. Countries worldwide have GMP regulations that regulate the production, verification, and validation of manufactured products.
Enforcement of Good Manufacturing Practice in the United States—Food and Drug Administration (FDA)
In the United States, GMP is enforced by the FDA through Current Good Manufacturing Practices (cGMP). These cover a variety of industries, including cosmetics, food, medical devices, and prescription drugs.
The FDA’s portion of the Code of Federal Regulations (CFR) is Title 21. This includes the Federal Food, Drug, and Cosmetic Act and related statutes, including the Public Health Service Act. Directives related to pharmaceutical or drug quality-related regulations appear in several Parts of Title 21, including Sections in parts 1-99, 200-299, 300-499, 600-799, and 800-1299.
Within these Sections are a few Parts of particular importance as related to good manufacturing practice are:
- 21 CFR Part 210—current good manufacturing practice in manufacturing processing, packing, or holding of drugs
- 21 CFR Part 211—current good manufacturing practice for finished pharmaceuticals
- 21 CFR Part 212—current good manufacturing practice for positron emission tomography drugs
- 21 CFR Part 314—for FDA approval to market a new drug
- 21 CFR Part 600—biological products
Global Enforcement of Good Manufacturing Practice
- Australia—Therapeutic Goods Administration
- Canada—Health Canada
- China—China Food and Drug Administration
- Europe—European Medicines Agency
- India—Central Drug Standard Control Organization
- Japan—Japan - Pharmaceuticals and Medical Devices Agency
- World Health Organization (WHO)—WHO Good Manufacturing Practices
GMP Guidelines
GMP guidelines and regulations require manufacturers, processors, and packagers of drugs, medical devices, and food to ensure that their products are safe, pure, and effective. There are ten steps that should be taken in order to follow good manufacturing practice.
These focus attention on five key elements, or the five Ps, of GMP—people, premises, processes, products, and procedures (or paperwork).
1. Create and distribute standard operating procedures (SOPs)
These should be step-by-step instructions that document all procedures and methods that should be followed when performing specific operations. The SOPs should be written clearly, concisely, and logically so that they are easy to understand. These SOPs should be provided to all employees along with a review to ensure that they are understood.
2. Implement and enforce the SOPs
All SOPs and work instructions should be embedded in employees’ workflows to ensure a controlled and consistent performance. Oversight should be in place to prevent shortcuts or deviations from the SOPs.
3. Document work
Documentation of work with regards to following SOPs should be prompt, and accurately created documentation provides an official record that is helpful for compliance. In the event of an issue, these records can support an investigation.
4. Validate work
Validate the effectiveness of SOPs by establishing documentary evidence that procedures, processes or activities, and production adhere to compliance requirements at every stage. This provides proof of consistent performance that follows written procedures.
5. Integrate productivity, quality, and safety into facilities design and equipment placement
Design with function, per the SOPs, in mind. Facilities’ design and construction should be done in a way that utilizes space and equipment for optimal productivity, quality, safety. This includes physically separating tools and materials to minimize confusion, cross-contamination, and potential quality issues.
6. Maintain equipment, facilities, and systems
Maintenance should be performed according to an approved schedule. All maintenance of equipment, facilities, and systems should be backed up with documentation that details what is done along with any issues or concerns related to safety or quality.
7. Foster job competence
Requirements for job competency should be clearly defined with associated procedures documented or called out in SOPs. Training should be provided to assure that requirements are understood and executed correctly.
Job competency should be based on consistently and efficiently producing a quality product. Achievement of and continued adherence to requirements for job competency should be documented.
8. Embed cleanliness in all activities
One of the easiest, most effective ways to prevent contamination is cleanliness. Cleaning and sanitization, as well as personal hygiene procedures, should be part of SOPs and enforced.
9. Build quality into workflows
Quality should be embedded in every step in the product development lifecycle, including controlling components, manufacturing, packaging and labeling, and distribution. A master record should be kept for every product with documentation of quality controls that were in place and details about how they were followed.
10. Conduct internal audits
Regular internal audits should evaluate good manufacturing practice compliance and performance. This not only identifies potential issues, but helps be prepared for external GMP audits.
What Is cGMP?
cGMP is an acronym that came from the FDA. It means current good manufacturing practice. The goal was to make clear to manufacturers that continuous improvement in their approach to product quality was important. Manufacturers should stay vigilant with regards to changes or improvements that could impact product quality—that is, stay current with good manufacturing practice.
Most other countries assume that manufacturers will keep abreast of changes to good manufacturing practice guidelines. Therefore, they do not use cGMP. This is why cGMP and GMP are often used interchangeably.
Audits and Inspections
The agencies that regulate good manufacturing practice around the world are authorized to perform audits and inspections to confirm compliance with GMP. Whether performed internally or by external groups, audits and inspections help not only to ensure quality, but also to improve the performance of different systems, including the following:
- Building and facilities
- Customer service
- Manufacturing
- Materials management
- Packaging and identification labeling
- Personnel and GMP training
- Purchasing
- Quality control systems
- Quality management systems
The stakes are high with agency-led inspections and audits. If serious violations are found, the FDA has the authority to recall products.
A few measures that can be taken to uphold good manufacturing practice standards and be prepared for audits and inspections are as follows.
- Appoint a quality team that focuses on enforcing and enhancing current manufacturing procedures and complying with good manufacturing practice.
- Demonstrate that instruments, processes, and activities are regularly evaluated by documenting evaluations. Among the areas that require validation in the event of a good manufacturing practice audit are the following processes:
- Process validation
- Cleaning and sanitation validation
- Computer system validation
- Analytical method validation
- Conduct internal audits to gain insights into day-to-day operations and identify areas of non-compliance.
- Provide compliance training to help staff better understand good manufacturing practice and give them the tools and skills to continually improve operations or systems according to GMP standards.
Good Manufacturing Practice Benefits Consumers and Organizations
Good manufacturing practice guidelines do not provide specific instructions for manufacturing. Follow recommended protocols, although they can sometimes be cumbersome and difficult.
This set of general principles helps organizations drive the most effective and efficient quality process. In addition to ensuring consistent, acceptable product quality and safety, a well-executed good manufacturing practice can:
- Reduce risks
- Save money
- Protect reputations
- Create a competitive edge
- Drive profits
Implementing and following good manufacturing practice benefits consumers and organizations.
Egnyte has experts ready to answer your questions. For more than a decade, Egnyte has helped more than 16,000 customers with millions of customers worldwide.
Last Updated: 23rd February, 2022
